Ensuring Reliable Power Supply Diesel Generator Commissioning Inspection
Introduction
Diesel generators play a crucial role in providing backup power during unexpected outages or in areas where a reliable power supply is essential. To ensure the reliability and optimal performance of a diesel generator, it is imperative to conduct a thorough commissioning inspection before putting it into service. This article will delve into the importance of commissioning inspections for diesel generators, the key steps involved in the process, and the benefits of adhering to proper inspection protocols.
Importance of Commissioning Inspection
Commissioning inspection is a critical phase in the lifecycle of a diesel generator as it ensures that the unit is installed correctly, functions as intended, and meets safety standards. By thoroughly inspecting the generator before it goes into operation, potential issues can be identified and rectified early on, preventing costly breakdowns and downtime in the future.
One of the primary reasons why commissioning inspection is crucial for diesel generators is to validate that the unit complies with manufacturer specifications and industry standards. Manufacturers provide specific guidelines for the installation and commissioning of their generators to guarantee optimal performance and longevity. Deviating from click this can result in reduced efficiency, increased maintenance requirements, and even safety hazards.
Additionally, commissioning inspection helps in verifying that all components of the diesel generator are functioning correctly and are in good condition. This includes checking the engine, alternator, fuel system, cooling system, exhaust system, control panel, and other essential parts of the generator. Any defects or deficiencies discovered during the inspection can be addressed promptly to ensure that the generator operates reliably when needed.
Key Steps in Diesel Generator Commissioning Inspection
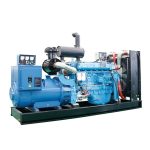
A comprehensive commissioning inspection of a diesel generator involves several key steps that should be carried out systematically to ensure thoroughness and accuracy. The following are the essential steps involved in the commissioning inspection process:
1. Physical Inspection:
The first step in the commissioning inspection is to conduct a visual inspection of the diesel generator and its components. This includes checking for any signs of damage, corrosion, leaks, or loose connections. Inspecting the generator in its entirety helps in identifying any visible issues that may impact its performance or safety.
2. Electrical Testing:
Once the physical inspection is completed, the next step is to perform electrical testing to ensure that the generator is properly wired and functioning correctly. This involves checking the voltage output, frequency, and phase rotation of the generator to confirm that it meets the required specifications.
3. Load Bank Testing:
Load bank testing is essential to verify the performance of the diesel generator under varying load conditions. By subjecting the generator to a simulated load using a load bank, its ability to handle different levels of power demand can be evaluated. This test helps in determining the generator's capacity and efficiency under real-world operating conditions.
4. Fuel System Inspection:
The fuel system of a diesel generator is critical for its operation, and any issues with the fuel supply can lead to generator failure. During the commissioning inspection, the fuel tanks, fuel lines, filters, and injectors should be inspected for cleanliness, leaks, and proper functioning. It is also important to ensure that the fuel quality meets the specifications recommended by the manufacturer.
5. Cooling System Check:
Proper cooling is essential for the efficient operation of a diesel generator, especially during extended periods of use. Checking the coolant levels, radiator, hoses, and fans is crucial to prevent overheating and ensure optimal performance. Any leaks or blockages in the cooling system should be addressed promptly.
6. Control Panel Testing:
The control panel is the brain of the diesel generator, responsible for monitoring and controlling its operation. During the commissioning inspection, the control panel should be tested to verify that all alarms, gauges, switches, and sensors are functioning correctly. Additionally, the settings and configurations of the control panel should be checked to ensure they are aligned with the generator's specifications.
7. Exhaust System Inspection:
Proper ventilation and exhaust of combustion gases are essential for the safe operation of a diesel generator. The exhaust system, including the muffler, piping, and silencer, should be inspected for leaks, blockages, and compliance with safety regulations. Adequate ventilation should also be ensured to prevent the buildup of harmful gases within the generator enclosure.
Benefits of Proper Commissioning Inspection
Adhering to proper commissioning inspection protocols for diesel generators offers a multitude of benefits that contribute to their reliable operation and longevity. Some of the key benefits of conducting thorough commissioning inspections include:
1. Enhanced Reliability:
By identifying and rectifying potential issues during the commissioning inspection, the reliability of the diesel generator is significantly improved. Ensuring that all components are functioning correctly and that the generator meets manufacturer specifications reduces the likelihood of unexpected failures and downtime.
2. Increased Efficiency:
A properly commissioned diesel generator operates more efficiently, delivering consistent power output and consuming fuel optimally. Regular commissioning inspections help in maintaining the efficiency of the generator by detecting and addressing any factors that may impact its performance.
3. Extended Lifespan:
Regular maintenance and commissioning inspections play a vital role in extending the lifespan of a diesel generator. By addressing minor issues early on and conducting preventive maintenance tasks, the wear and tear on the generator's components can be minimized, leading to prolonged service life.
4. Compliance with Safety Standards:
Ensuring that a diesel generator undergoes a thorough commissioning inspection helps in complying with safety standards and regulations. By verifying that the generator is installed and functioning in accordance with industry guidelines, the risk of accidents, malfunctions, and environmental hazards is mitigated.
5. Cost Savings:
Proactively conducting commissioning inspections can result in cost savings in the long run by preventing major breakdowns, repairs, and downtime. By investing in proper inspection and maintenance practices, unnecessary expenses associated with emergency repairs or replacements can be avoided.
Conclusion
In conclusion, the commissioning inspection of a diesel generator is a critical process that ensures its proper installation, functionality, and compliance with safety standards. By following the key steps outlined in this article and adhering to manufacturer guidelines, the reliability, efficiency, and longevity of a diesel generator can be maximized. Investing time and resources in thorough commissioning inspections not only enhances the performance of the generator but also contributes to a reliable power supply when it is needed the most.